3Dプリンター3Dプリンターの代表的な方式や材料と、導入のメリット
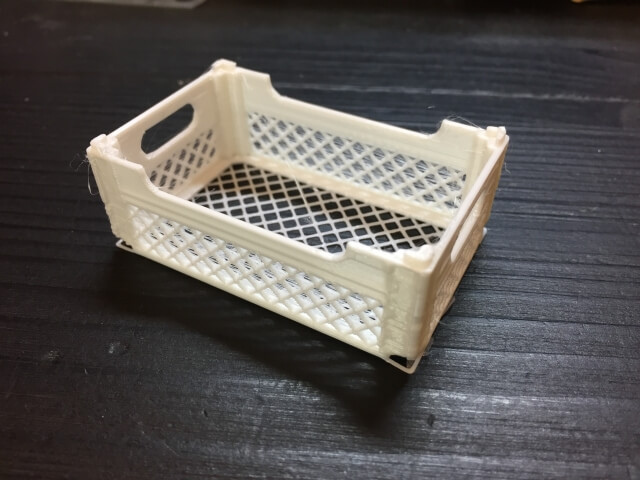
近年のテクノロジーの進歩によって、3Dプリンターの性能が向上し、種類も増えてきています。
業務用だけでなく、家庭用のアイテムもリリースされているため、幅広い分野に浸透してきているといえるでしょう。
しかし、「3Dプリンター」とはいっても、その種類や使用される材料には様々な種類があります。
3Dプリンターを導入する際には基本的な知識を抑え、自社にとって最も望ましい導入方法を考えることが大切でしょう。
この記事では、3Dプリンターとは何かについて、方式や材料、メリットといった観点から解説します。
もくじ
3Dプリンタとは
まず「3Dプリンタ」とは、パソコンで作ったデータを立体物としてプリントアウトするための機械のことです。
つまり一般的なプリンターが平面的な「2D」であるのに対し、3Dプリンタでは「3D」の立体物をプリントアウトできるということ。
3Dプリンタではパソコンでデータを設計した後に、作成した設計図の通りに実物として立体物を印刷できます。
印刷の方法は、2Dであるスライスされた平面の像を、3Dになるように何枚も立体的に重ねていく方法が採用されています。
層を重ねながら印刷した後は、紫外線を使って液体化された樹脂を固めたり、熱で溶かされた樹脂を固めたりする方法により硬化。
実際にある既存製品のデータをパソコンに取り込んだとしたら、全く同じ製品を複製することも可能です。
パソコン上で設計図とデザインが完成していれば、3Dプリンタを通してそのまま製作ができます。
従来の方法で製品を制作するよりも、圧倒的に時間や工数を節約できることがおわかりいただけるはずです。
3Dプリンターの方式
ここでは、3Dプリンターの代表的な方式について解説します。
FDM方式
FDM方式とは「Fused Deposition Modeling」の略であり、日本語では熱溶解積層方式と呼びます。
樹脂を高温で溶かし、プリンターヘッドから出して積み重ねることで対象物をモデリングしていく方式です。
2009年に特許が切れ、現在は非常に安価で導入できるプリンターの方式です。
材料も現在主流のものが使用できるため、ランニングコストが抑えられる方法でしょう。
精度や仕上がりが荒いといわれることもありますが、近年は技術の進歩によって徐々に改善されてきています。
FDM方式の仕組みやメリットについてさらに詳しく知りたいという方は、コチラの「FDM方式とは。仕組みやメリットについて解説」の記事をご覧ください。
光造形方式
液体樹脂を紫外線で加工する積層方式です。
複雑な形のモデリングでも精度高く仕上げることができ、数ある方式の中でも最も普及しているため、信頼性も高いと考えられるでしょう。
しかし、仕上がりまでに時間が掛かるため、量産には向いていません。
本体や材料の価格が高く、コストパフォーマンスが悪い点もデメリットです。
高精度の大型造形には、光造形方式が向いているとイメージしておくとよいでしょう。
光造形方式について詳しく知りたいという方は、コチラの「光造形3Dプリンターの特徴と導入時のメリット・デメリット」の記事をご覧ください。
粉末焼却積層造形方式
「粉末焼結積層造形方式」はパウダーにした材料を焼いて固めていくタイプです。
印刷された造形物は微細性や審美性には少々劣るものの、強度は他の方式の印刷よりも勝ります。
耐久性が高い造形物を作成できることと、金属素材による造形が可能であることが大きなメリットです。
鋳型を製造する用途にも活用できるため、ものづくりのシーンで大きな活躍が期待できるタイプだと言えるでしょう。
3Dプリンタでは、宙に浮いた部分であるオーバーハングによる造形中の垂れが問題になることもあります。
しかし粉末焼却積層造形方式では樹脂の場合に土台となるサポート剤が不要で、オーバーハングすると思われる造形に最適です。
完成物はざらついた質感の表面となります。
使用される素材はナイロンもしくは金属が主。
パウダー状の材料を焼き固めていく「粉末焼却積層造形方式」は、鋳型製造などものづくりの分野に適しています。
インクジェット方式
通常のプリンターでも有名なインクジェット方式は、3Dプリンタでも採用されています。
3Dプリンタにおけるインクジェット方式とは、インクの代わりに樹脂を噴射しながら造形を行う方式です。
他の方式に比べ比較的新しく、従来の方式よりも表面の質感がなめらかで、微細に造形できることが最大の特徴。
通常のインクジェットプリンターと同じように、フルカラーでの造形が可能であることもメリットのひとつでしょう。
造形の精細さが魅力のインクジェット方式ですが、作業時間は他の方式に比べて短いにも関わらず複雑な形状も作成可能。
表現力と審美性の両方を兼ね備えているのがインクジェット方式の魅力です。
粉末接着方式
「粉末接着方式」とは回転テーブルの上に石膏の粉末を敷く方式の3Dプリンタです。
プリンタヘッドから出る液体接着剤が石膏の粉末を固めることにより、3Dの造形物を作り出す仕組みとなっています。
粉末接着方式で使用される接着剤はCMYKインクで着色されているので、フルカラーの造形物を作り出すことが可能。
色彩豊かな造形物を作り出すときに最適な方式です。
しかし石膏は素材として脆いという特徴を兼ね備えています。
そのため完成した造形物の強度はそれほど高くなくなります。
さらに完成品の表面がざらつくこと、精度が低くなることなどが粉末接着方式のデメリットだと言えるでしょう。
3Dプリンターの材料
ここでは、3Dプリンターに使用される代表的な材料を紹介します。
PLA樹脂
トウモロコシやジャガイモのでんぷんによって造られた、環境に優しい熱可塑性樹脂です。
比較的安定性が高く、冷却しても変形やゆがみが発生しにくい点がメリットです。
しかしその逆に高温には弱く、衝撃にも弱い点はデメリットでしょう。
表面は堅くて丈夫ですが、造形後の塗装ややすり掛けなどといった後加工には不向きな樹脂です。
樹脂が溶けたような嫌な臭いがせず、大きな造形物の制作に向いています。
ABS樹脂
剛性や耐衝撃性、疲労強度などのバランスがよく、後加工にも適している汎用熱可塑性樹脂です。
アクリロニトリルとブタジエン、スチレンの3種類の有機化合物を結合させてできており、電解製品の外装部品などに広く使われています。
ただし、気候変化には弱く、太陽光に長時間当たることで強度の低下につながったり、湿気で変形してしまったりすることもあります。
冷却すると反ってしまうことが多く、大きな造形物にはあまり向いていないといえるでしょう。
ASA樹脂
ABSを構成している化合物の1つであるブタジエンをアクリレートに置き換えた熱可塑性樹脂です。
基本的な特徴はABS樹脂と同じですが、より天候の影響を受けにくくなり、屋外使用への適性が高まった素材です。
PP樹脂
PP樹脂は熱・衝撃に強く、軽量であることが特徴の材料です。
耐熱容器として頻繁に使用されていることからも、熱への耐性が高いことがわかります。
また耐薬品性にも優れていることから、医療業界での活躍も期待される材料です。
従来では「粉末焼結方式」で使用されること多い材料でした。
しかし最近では「熱溶解積層方式」で使用できるPPM樹脂フィラメントも販売されており、今後さらに広い用途で活用できるようになるでしょう。
PET/PETG
PETとPETGはいずれも、熱に強く耐久性に優れる材料です。
ペットボトルの素材として利用されているのがPETであり、非常に身近な素材だと言えるでしょう。
PETよりさらに強度を高くしたのがPETGです。
いずれの素材も強度・耐久性・耐熱性に優れ透明度の高い素材。
しかし造形した完成品では、少々透明度が低下することに注意が必要です。
透明感を求めるならPETよりPETGを利用するのがおすすめ。
いずれにしても耐熱性と耐久性に優れる素材です。
エポキシ系樹脂
エポキシ系樹脂は、熱により硬度が増すことが特徴的な材料です。
エポキシ系樹脂では「ABSライク」「PPライク」の2種類の素材が一般的ですが、いずれも光造形方式の3Dプリンターで活用されています。
名前の通り「ABS樹脂」や「PP樹脂」と同じように利用できますが、強度に関してはそれぞれの樹脂の方が勝ります。
強度を求める造形物では、エポキシ樹脂よりもABS樹脂・PP樹脂を利用した方が良いでしょう。
どちらの素材も造形した後の安定性が高く、耐薬品性が高いことから医療・薬品分野で利用される造形物の作成におすすめです。
アクリル樹脂
熱を加えることにより軟化・溶解するタイプの透明度の高い材料のことです。
メリットは衝撃と屋外の環境に強いこと。
メリットを活かして建材・車輌などに活用されることが多い材料です。
しかし3Dプリンタで造形すると透明度が少々低くなることと、表面に傷が付きやすいことがデメリットとなります。
そのため審美性よりも耐久性を求める造形物と相性の良い材料です。
PC樹脂
PC樹脂とはポリカーボネートが原料となる耐久性・耐熱性に優れたエンジニアリングプラスチックのこと。
PETやPETGなどもプラスチック材料ですが、数あるプラスチックの中で最も耐久性に優れるのがPC樹脂です。
PC樹脂は非常にメリットの多い材料で、まとめると次のようなメリットがあります。
- プラスチック材料の中でも最も強度が高い
- 耐熱性に優れている
- 耐衝撃性に優れている
- 耐候性に優れている
- 軽量である
- 研磨により光沢が出る
上記のように審美性・耐久性・軽量性に優れる材料です。
しかし高温多湿の環境で使用するには適していません。
また利用できる機種が少ないこともデメリットと言えるでしょう。
耐久性・耐熱性を求めるプラスチック製造形物とは相性の良い素材です。
ナイロン樹脂
ナイロン樹脂もPC樹脂と同じくエンジニアリングプラスチックの一種です。
3Dプリンタにおける特徴は、耐衝撃性・耐熱性・耐薬品性に優れていて柔軟であること。
一般的には粉末焼結方式で活用されることが多く、熱溶解積層方式では利用されません。
PC樹脂は研磨により光沢が出ますが、ナイロン樹脂はテクスチャがざらついていることが特徴のひとつ。
エンジニアリングプラスチックで造形を行う際に選択肢となり得るのがナイロン樹脂です。
熱可逆性ポリウレタン
熱可逆性ポリウレタンは食品・医療の業界でよく用いられる3Dプリンタの材料です。
主にゴムやエラストマーが熱可逆性ポリウレタンとなります。
熱に強くやわらかで、厚みを増すごとに硬さが増す特徴があり、着色可能であることがメリットです。
しかし造形物の安定性は高くなりません。
熱可逆性ポリウレタンを利用できる機種も限られているため、活用の機会は低くなりがち。
食品・医療業界で造形を行いたい場合に適する材料です。
石膏
石膏は粉末状の材料で、模型・フィギュアの作成前確認として用いられることが多い材料です。
材料の特性として耐久性が低く壊れやすいため、実際に造形物を作るための材料としては不適切でしょう。
しかし価格が安く、すばやく造形できることから本番前の確認用としては最適な材料です。
着色もできるので、模型・フィギュアのイメージを確認するために適します。
ただ石膏を利用できる3Dプリンタはバインダージェット方式のみであるため、事前に利用できるか機種を確認しておくことが必要です。
以上のように石膏は模型・フィギュアを実際に造形する前の確認用としておすすめの材料です。
ゴム
ゴムは先に解説した熱可逆性ポリウレタンの中に含まれる材料です。
ゴムはエラストマーとも呼ばれる材料で、摩耗や衝撃に強く、やわらかで引っ張っても切れにくい特徴を持ちます。
ねじったり曲げたりしても折れることはなく、柔軟性に優れています。
その他の特徴やメリット・デメリットは熱可逆性ポリウレタンの項目で解説したとおりです。
金属
3Dプリンタの材料として金属も使用できます。
金属であればほとんどの材料を使えますが、鉄や銅に加え、ニッケル・チタン・ステンレス・アルミニウムなどが用いられます。
種類により変わりますが、ステンレスや鉄などは強度が高いことがメリットです。
そのため石膏のようなテスト段階の造形ではなく、最終的に製品を製造する段階で用いられることが多くなっています。
強度の高い造形物を作成した場合は、材料として金属を用いてみてはいかがでしょうか。
3Dプリンターを導入するメリット
ここでは、3Dプリンターを導入するメリットについて解説します。
コスト削減
まず挙げられるのが、コスト削減効果です。
それまで外部の組織に発注していたものを社内でできるようになるため、その分コストを削減できます。
試作品の製造・確認を社内で行えるため、ミスが減って無駄なコスト発生を避けることができるでしょう。
開発時間の削減
開発時間の削減も、非常に大きなメリットです。
これまで金型を作成してから造形していたものが、データさえあればすぐに作成できるようになります。
試作品やテストパーツなどを簡単に作れるようになることで、開発時間を大幅に削れるでしょう。
品質の向上
モデリングが容易にできることから試作段階で細かい確認ができ、量産する前に事前検証を行うことで最終的な品質の向上につながります。
1つのかたまりとして出力できるため、従来のものと比較して耐久性にも優れたものが期待できるでしょう。
3Dプリンタを導入するデメリット
3Dプリンタを導入することにはメリットだけではなく、次のようなデメリットもあります。
デメリット1:3Dデータの作成が必要
3Dプリンタで造形物を作るには、3Dデータを作成しなければなりません。
これまでも3Dデータを作成していたとのことでしたらデメリットにはならないはずです。
しかし今まで3Dデータを作成したことがない方にとっては、データの作成をするより、直に製品を作る方が簡単である場合もあるでしょう。
3Dプリンタで造形物を作成するためには3Dデータが必要です。
3Dデータを作成するための技術や学習が必要となることはデメリットとなりえます。
デメリット2:完成品の耐久性が低下
完成品の耐久性が低くなりがちであることも3Dプリンタ導入のデメリットです。
3Dプリンタの材料の中には、金属やエンジニアリングプラスチックなど耐久性に優れた材料もあります。
しかし分野によっては、従来の方法で作成したほうが耐久性が高くなることもあるでしょう。
そのため模型・フィギュアの確認段階や、試作段階でしか3Dプリンタを活用できなくなることも考えられます。
導入を検討されているなら、従来より造形物の耐久性が低くなる可能性があることを知っておいてください。
3Dプリンタの活用シーン
3Dプリンタにはデメリットもありますが、現在では幅広い分野で活用されていることも事実です。
それでは3Dプリンタはどのようなシーンで活用されているのでしょうか。
代表的な活用シーンをいくつかご紹介していきます。
活用シーン1:作品の完成度確認
まずは作品の完成度を確認するために活用されている事例です。
3Dプリンタで開発する商品の試作品を作ります。
そして問題点やさらなる改善点がないか確認し、最終的に製作される作品の品質を高めるために活用。
3Dプリンタでは手触りまで表現できるので、作品の完成度を忠実に再現するために役立ちます。
活用シーン2:模型によるプレゼンテーション
プレゼンテーションで使用する模型で3Dプリンタを活用している方もいます。
設計図や図面だけでは完成品の雰囲気を伝えるのは難しいものです。
特に建設業界や建築業界では、プレゼンテーションの際に設計を忠実に再現した模型を用いることで印象アップを狙えます。
3Dプリンタであればわずか数日で模型を作れることもあり、製作のための工数や時間を大幅に短縮可能。
プレゼンテーションでの訴求効果も高まるため、非常に有効に活用できるはずです。
活用シーン3:設計の確認
3Dプリンタによる造形は、設計の確認のためにも活用されています。
試作品の作成や最終的な製品製造段階前の確認には、3Dプリンタによる造形物が役立つためです。
3Dプリンタで実物と同様の造形物を作れば、たとえば製品の部品同士が干渉して不具合を起こさないか容易に確認できます。
造形物での確認により設計段階でのミスを早期に発見できれば、最終的な製造はよりスムーズに進むはずです。
活用シーン4:型の製造
型の製造で3Dプリンタを利用している事例も多く見られます。
これまでの方法では型を製造するために高額な費用と日数が必要とされました。
しかし3Dプリンタを活用すれば、大幅にコストダウンさせながら、簡単に型を製造できるようになるのです。
製造するための日数も1日だけで済むでしょう。
3Dプリンタで作れる型は樹脂製・金属製と幅広く、製造業における活用シーンは幅広いはず。
3Dプリンタは試作品作成や最終的な製造の確認のためだけでなく、型を製造するシーンでも役立ちます。
3Dプリンターの技術はこんなところに用いられています
ここまでは3Dプリンターの特徴や、導入することで得られるメリットについて紹介しました。 しかし実際に一般レベルでも3Dプリンタ―が使われるようになってきているとはいえ、具体的にどういった業界で・どういった使われ方をしているのか、という部分までしっかりと理解している方は少ないのではないでしょうか。 昨今では医療や教育といった現場でも活用されていることをご存知でしょうか。 そこで当社のサイトではそうした3Dプリンターの用途についても詳しく紹介しております。
具体的な3Dプリンタ―の使い道について興味のある方は、コチラの「3Dプリンターの使い道を代表的なものから意外なものまで紹介」の記事をご覧ください。3Dプリンターの導入を検討しよう
今回は、3Dプリンターの概要について解説してきました。
自社にとって3Dプリンターが必要か、判断する材料となりましたでしょうか?
3Dプリンターを導入することで、開発期間・コストの削減や品質の向上につながるでしょう。
フュージョンテクノロジーでは、高性能機種やリーズナブルなものまで、さまざまな3Dプリンターをご提供しています。
3Dプリンターについてのご相談はぜひ株式会社フュージョンテクノロジーまでお寄せください。